Modular remote I/O systems transmit process data from safe or explosion hazardous areas by connecting binary and analog sensors and actors to the control system via a bus interface.
You can connect 4 mA … 20 mA devices to remote I/O, including water flow transmitters, valve positioners, pressure transducers, or temperature transmitters. Devices such as thermocouples, resistance temperature detectors (RTDs), mechanical contacts, and visual or audible alarms may also be connected. Our remote I/O systems are compatible with network protocols like PROFIBUS DP, PROFINET, MODBUS RTU, MODBUS TCP/IP and others.
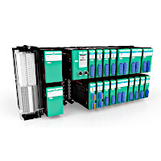
FB remote I/O is certified for mounting in Zone 1, placing the remote I/O system close to field devices. This modular signal conditioning system allows you to interface signals from the field with a control system located in the non-hazardous area via the following connections:
- Intrinsically safe field connections (Ex i)
- Increased safety field connections (Ex e)
The FB remote I/O system is installed in an enclosure. Standard enclosure options are glass fiber reinforced polyester (GRP), fiberglass, or stainless steel. Pepperl+Fuchs offers complete remote I/O solutions, including fully certified enclosures with built-in systems and components.
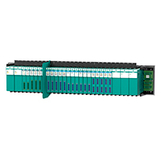
LB remote I/O is certified for mounting in Zone 2, Class I, Div. 2 or in the non-hazardous area. Thismodular signal conditioning system allows you to interface signals from the field with a control system in the non-hazardous area via the following connection types:
- Safe area field connections (Non-Ex)
- Intrinsically safe area field connections (Ex i)
Both circuit types can be mixed in one system. The LB remote I/O system is plugged into a backplane. Alternatively, our Solution Engineering Centers (SECs) can provide the system pre-mounted into a fully certified custom enclosure.